10 Core Trends Boosting Profitability in the Machine Economy
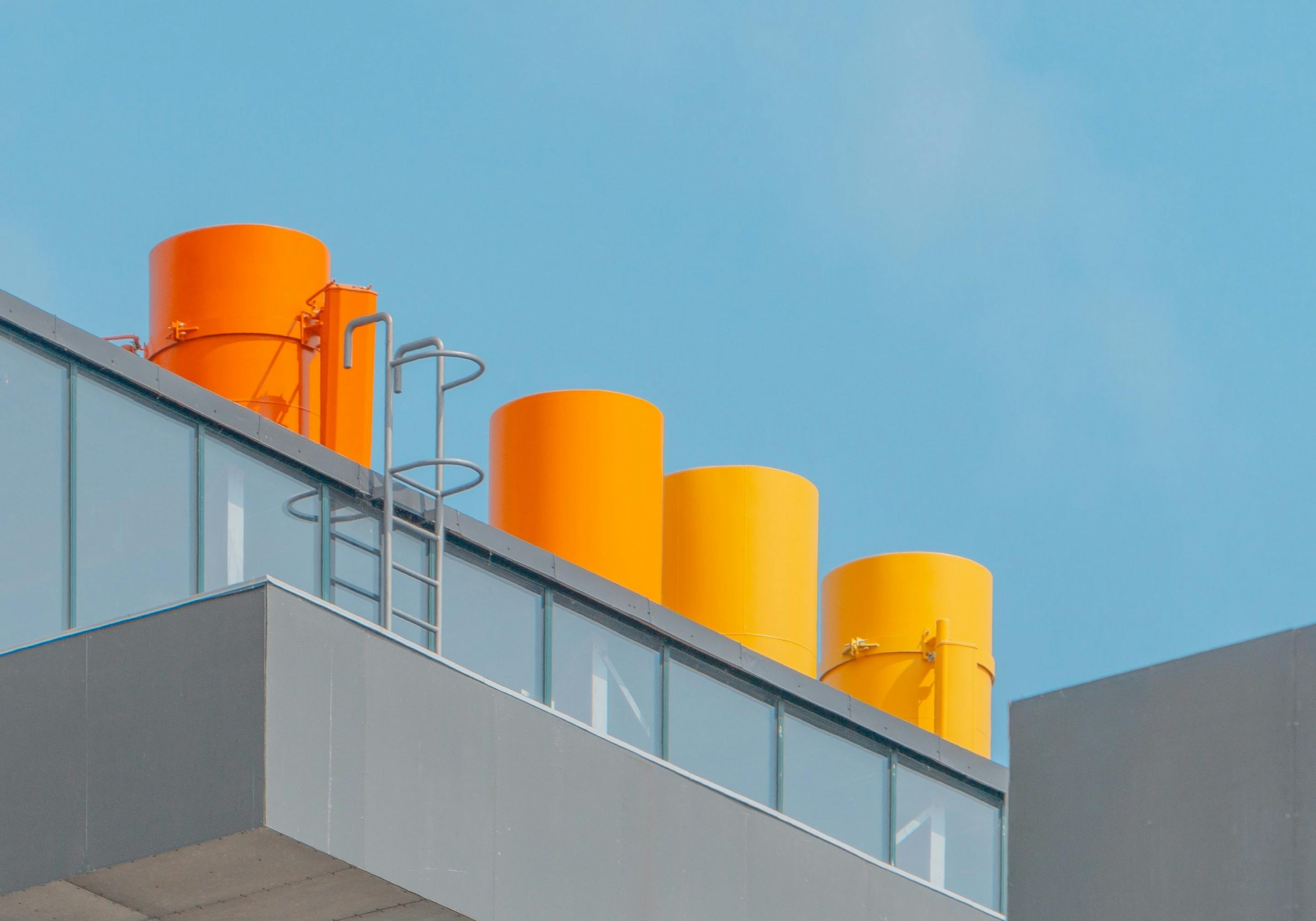
New business ideas are becoming increasingly sparse in today’s complex and saturated marketplace. Data is so omnipresent that, with just it alone, businesses have difficulty in setting themselves apart and maintaining a competitive edge.
The true value of data lies in what you can do with it; the actionable insights that it provides corporate leaders with to make better business decisions. Whether that business is a newcomer or market incumbent, these companies need to take data one step further and prioritize innovation to compete in the marketplace or ultimately face the risk of obsolescence.
Establishing an IoT infrastructure and commercializing the solution can be challenging, but when done correctly it can be a complete game-changer for companies. The IoT business model is tightly intertwined with the two adjacencies of product development and product commercialization. According to IoT Analytics, it typically takes 23 months for the average smart, connected IoT product to go from internal project kick-off to acquiring its first paying customer.
Although many examples of established IoT-enabled business models already exist, companies that are planning to bring IoT solutions to market should ask themselves: What can we learn from early innovators to create a sustainable and robust IoT business model?
Motivations and Trends Shaping the Machine Economy
People may be the driving force behind the economy, but the rise of IoT, blockchain and AI is establishing an entirely new category of economic activities without the need for human interaction: the Machine Economy.
The Machine Economy is built upon the principles of IoT business models: awareness, automation, and actionable insights. It’s critical to clearly understand the needs of the business (internal) and those of the consumer (external) before building and selling an IoT solution.
Today, most IoT solutions are found in the manufacturing and industrial sectors. IIoT (industrial internet of things) is transforming the rules of the production process, fueling cloud and edge innovation, accelerating the rise of digital lighthouse factories, and enhancing operational efficiency. Although the ‘as-a-service’ model is no longer a new phenomenon in manufacturing, it is gaining industry traction, especially since general observations indicate a decline in classic CapEx sales. In contrast to a one-off purchase, the subscription model is offering companies the opportunity to generate regular income streams throughout the entire lifecycle of the asset. By offering customers value-added services, companies can create additional points of contact, which leads to a closer relationship and improves customer satisfaction.
Currently, businesses prioritize digitalization (and a move toward the Machine Economy) for two main reasons:
- The development of new products and services
- The creation of new value streams through improved operational performance
With more than 7.2 billion machines as customers already in existence, the Machine Economy presents many opportunities that go beyond automating tasks that were originally performed by humans. From a corporate perspective, high-level business executives and technology experts have identified 10 key trends in the Machine Economy that will boost profitability. These trends are in specific reference, but not limited, to industries transacting with industrial suppliers, industrial engineers, automotive manufacturers, and material and processing industries.
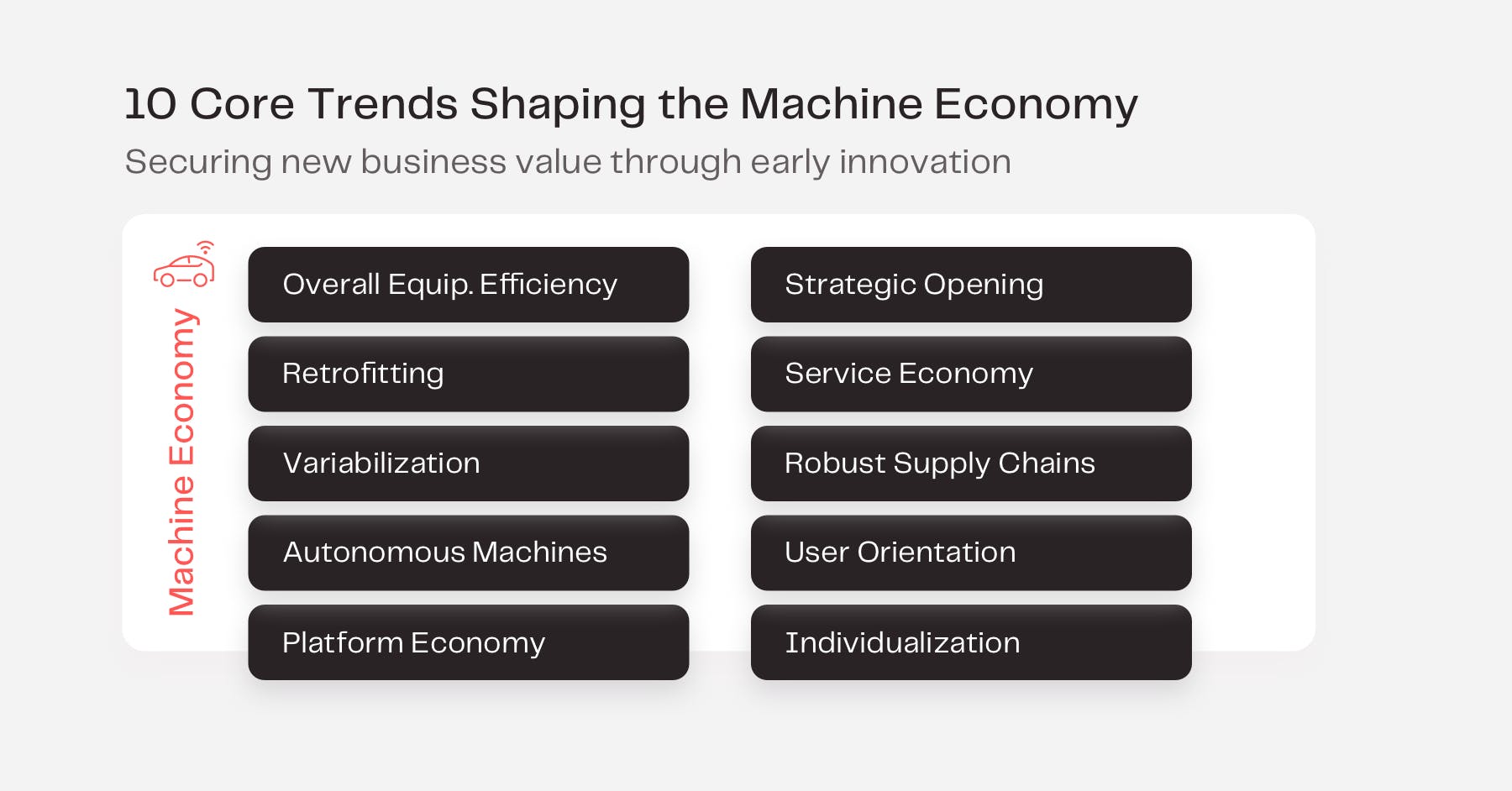
1. OEE
Overall equipment efficiency measures an asset’s level of productivity. The fundamental increase in efficiency will be one of the most important, if not the most important, trends for companies in the context of the Machine Economy.
OEE is a combination of three factors: asset availability, asset performance, and production quality.
- Availability – Does the asset function when needed?
- Performance – How many items does the asset produce?
- Quality – Does the asset produce consistent high-quality items?
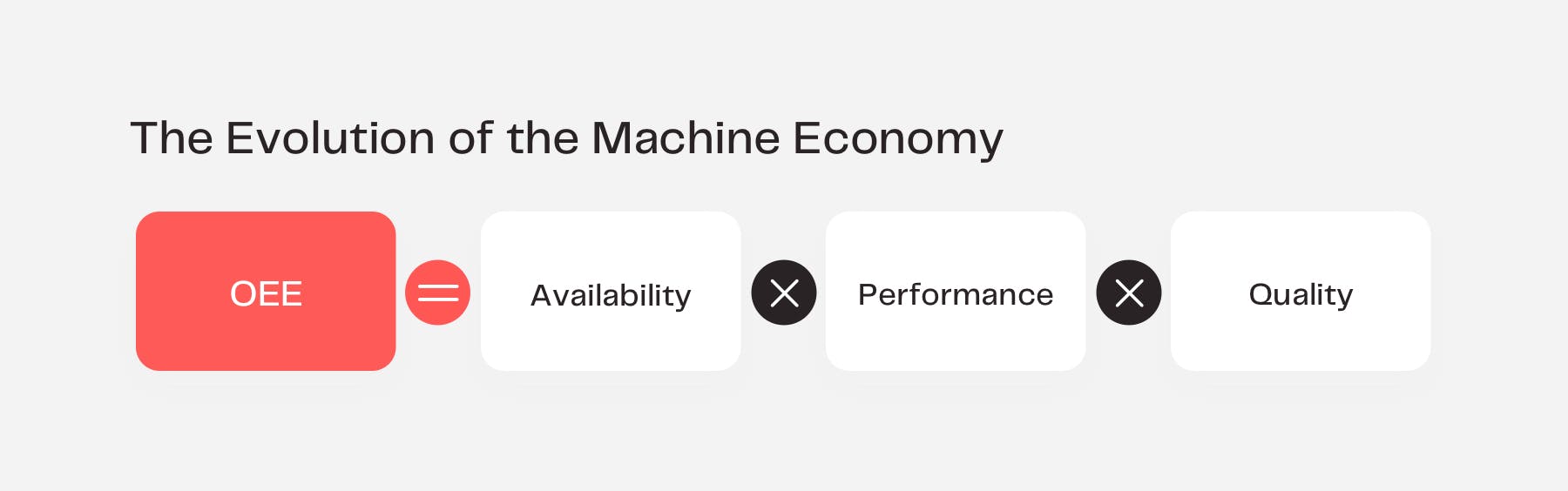
OEE provides valuable insight for production scheduling, organizing, and conducting maintenance tasks. This information helps companies predict maintenance needs, decrease downtime, and avoid common asset-related issues that cost organizations valuable time and money.
2. Strategic Opening
Open strategy forms part of a larger societal trend toward greater degrees of openness in all domains of life such as open innovation, open source software, open data, and open science. In recent years, companies have realized the limitations of only networking internal machinery. Instead, many companies are developing strategic alliances with venture studios, corporations, and ecosystem partners to promote innovation across the entire value chain.
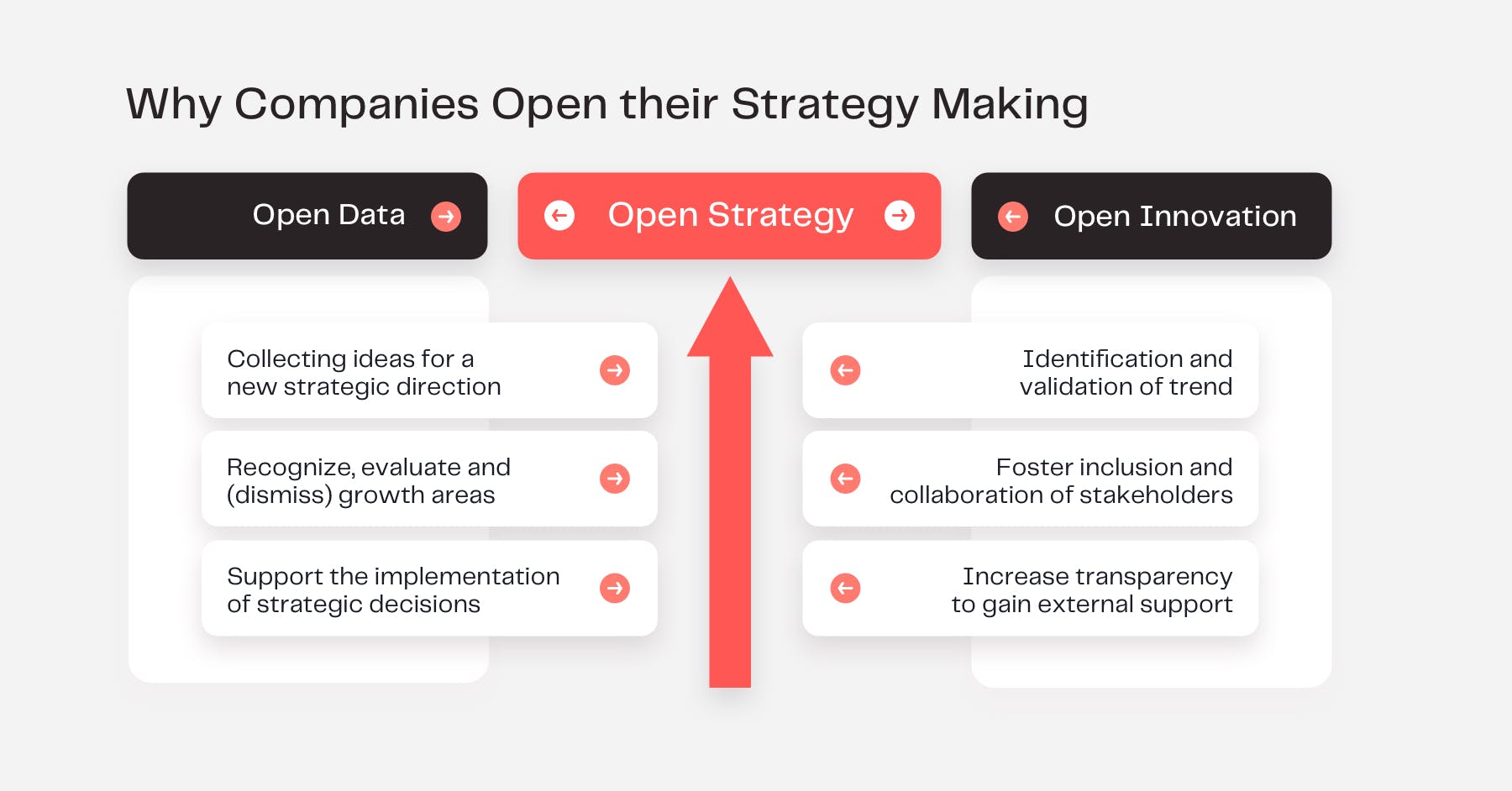
3. Flexibilization & Individualization
Manufacturing and production lines will be more flexible in the future to offer customers greater individualization based on specific user needs and preferences. Producing mass-customized consumer goods poses two main challenges: 1) To be cost-efficient, the production system must self-configure for any individual product design without the need for human involvement, and; 2) Any individual product must be quality-perfect since replacement parts will also be custom-made. Achieving these goals is possible using digital twin technology, machine learning algorithms, and M2M communication protocols. While many current individualized production requires a significant up-front investment, future solutions will transition toward annual OpEx investment strategies.
4. User Orientation
With the increasing complexity of technologies, the user experience will play an even greater role in the future. User-centered design is characterized as a multi-stage problem-solving process where manufacturers analyze and envision the way users are likely to consume a product or service. These assumptions are validated through user testing and iterations for future generations of products. For both factory staff and consumers, improved usability can be achieved through self-explanatory tutorials on devices or via AR and VR.
5. Robust Supply Chains
With the advent of unforeseen events, a resilient supply chain is needed to secure a constant supply of goods and services. Supply chains are no longer linear systems and are characterized by network structures with autonomous and heterogeneous members. Companies are fragmenting supply chains and shifting production activities to operate locally rather than relying on foreign manufacturing plants. This regionalization of supply chains means that if or when disruption occurs, any back-up supply can be deployed rapidly. Continuous technological developments in AR, warehouse automation, and 3D printing are aiding in supply chain resiliency.
6. The Service Economy
Selling physical products will not be enough for companies to remain competitive in the future. Market pressure from competitors with platform aspirations and first-mover market dominance is a major threat to slow tech adopters. As consumer needs become increasingly dynamic, businesses are pursuing servitization with the first stage of expansion shifting from product to solution distribution. Companies are transitioning from creating value through making and selling a product to combining a physical product with related services, such as the maintenance of machinery. In the future, machines will sell services-as-a-product to businesses paying per hour, per hectare, or per outcome, rather than purchasing the asset outright.
7. The Platform Economy
The creation of digital communities and platform marketplaces allows different groups to interact and transact. According to research published by McKinsey in 2019, 84% of traditional firms have their own platform or utilize one operated by a third party. The platform-enabled business model will dominate the logistics, manufacturing, and engineering industries. Blockchain technology will become integral to ensuring interoperability in traditional industries and in the coming years, we will see new platforms emerging around DLT (distributed ledger technology).
8. Autonomous Machines
Self-learning systems and advances in smart sensors enable machines to act autonomously in both the physical and digital worlds. Machines cooperate with one another to achieve greater speed and efficiency by exchanging information, distributing tasks, and coordinating their actions. Smart machines are made ‘smart’ with advanced computer programming and robotics that enable each machine to process vast amounts of data to make rapid and informed decisions. DLT is at the center of enabling machines with the necessary capabilities to perform tasks such as conducting transactions and concluding contracts.
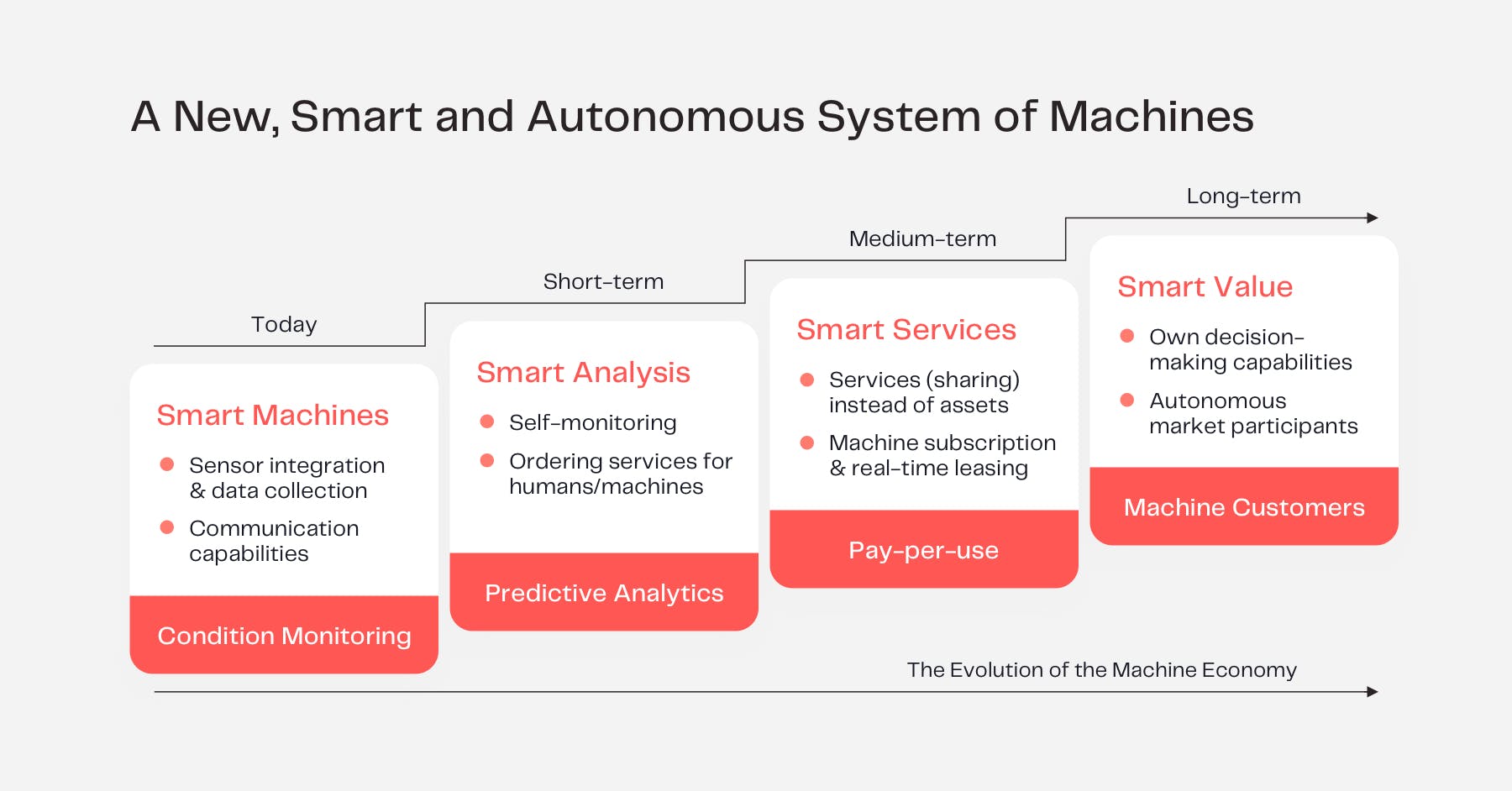
9. Variabilization
Why should you need to own an asset to use it? Variabilization is the transformation of fixed costs (CapEx) into variable costs (OpEx). There are two types of variabilization: 1) back-end variabilization, through which a company variabilizes its costs (outsourcing machinery, or transportation fleets), and; 2) front-end variabilization, in which a company designs offerings to variabilize its consumers’ costs (selling services per outcome, plus maintenance, plus replacement parts). More companies are dealing with pay-per-use models in which investments are no longer made directly in machines, but rather in the production output provided. As a result, companies’ costs are becoming more variable, making businesses more resilient through the strategic and agile allocation of capital.
10. Retrofitting
Manufacturers that want to participate in the Machine Economy will have to purchase new digital machinery or upgrade existing machinery and other legacy systems. However, purchasing new machines with smart technologies is often expensive and impractical for small and medium manufacturing companies. This is where retrofits offer a solution. Smart factory retrofit solutions enable an old machine or system to access new technologies. The details can be installed on an old machine or a particular part can be replaced by a new edition with improved features. A business that invests in retrofits and smart manufacturing can achieve the following:
- Lower production costs
- Reduced energy consumption
- Reduced environmental footprint
- Improved organizational efficiency
- New value streams
From Laggard to Leader
Gaining corporate buy-in for new technologies has been an age-old challenge, however, it’s time to question old business patterns and recognize new opportunities. Industrial players are finding new ways to reduce manufacturing costs and make production lines more flexible by engaging in adaptive operations. Combine this with the growing trend of servitization and automation, and manufacturers can spread their geographical focus by venturing into emerging markets in ways previously unimagined.
Although the Machine Economy may still be in its nascent phase, there has never been a better time for forward-thinking companies to take advantage of these 10 core trends.
The next few years will see a profound transformation of industrial processes, increasing the synchronization between different components in the value chain, and automated machine decision-making. Businesses that pursue digital transformation in a multi-dimensional way will outpace the rate of disruption and successfully leverage existing assets to become world-class corporate leaders.